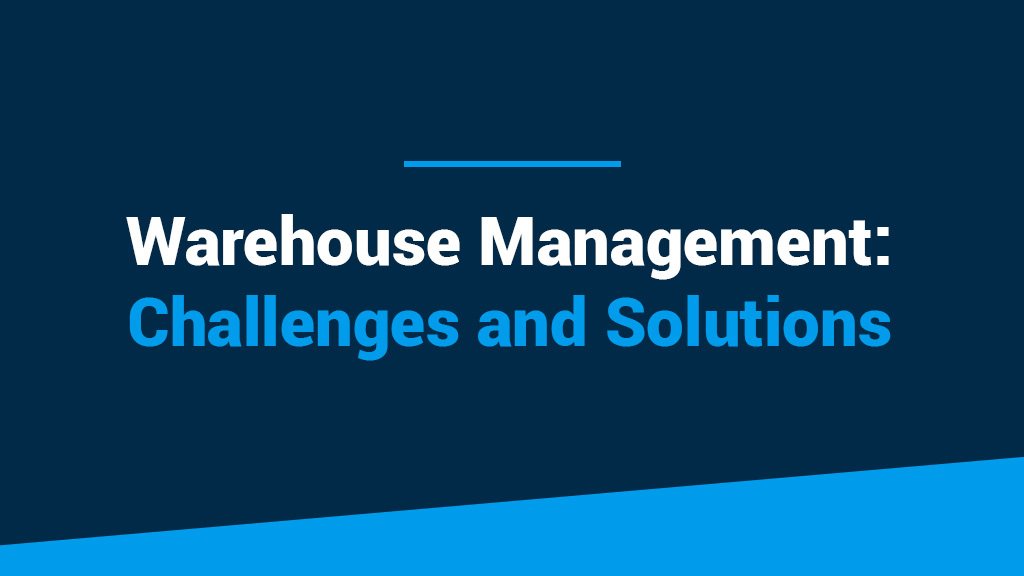
- Warehouse management oversees, organizes, and optimizes warehouse operations to ensure efficient, accurate, and cost-effective inventory handling.
- Skustack enables warehouse workers to pick orders with a high level of accuracy using mobile devices and gives warehouse managers a top-down view of warehouse activity.
Warehouse management is essential to running an efficient warehouse and an ecommerce business. It is crucial to maintaining order and helping companies outperform competitors. According to Myos, US inventory accuracy is estimated to be approximately 63%, implying a significant amount of inventory is unaccounted for.
However, navigating the solutions available to better manage warehouses can be complicated. It’s not always clear what defines warehouse management, and software solutions handling different warehouse operations can overlap in functionality.
Without a good system in your warehouse, you risk falling behind the competition that may already use a WMS. In this article, we will discuss why that can happen and what you can do about it.
What Is Warehouse Management?
In a nutshell, warehouse management is the practice of managing everything related to the warehouse. Broadly, this includes workers, warehouse processes, and monitoring. However, there is no agreement about what defines warehouse management. Because of this, solutions can vary, and businesses work differently depending on their needs.
The topic becomes further complicated as some tasks overlap with other ecommerce business areas. For example, it’s important to establish early on that warehouse management is often used interchangeably with ‘inventory management.’
While there is a lot of overlap between the two (both fall under ‘supply chain management’), there are some critical differences:
Warehouse management covers all the day-to-day operations of running and maintaining a warehouse, such as receiving inventory, organizing space, workforce management, picking, sorting, packing, and reporting. Warehouse management also includes monitoring and optimizing the many processes and workflows under its domain to improve efficiency and increase productivity.
Inventory management is focused on purchasing, storing, and moving inventory. It does not include managing workers or warehouse space. The most basic warehouse management tasks include:
- Order picking—Gathering products to fulfill customer orders.
- Packing—Preparing and packaging picked items for shipment.
- Storage—Organizing and keeping inventory in designated warehouse locations.
- Receiving—Accepting and inspecting incoming goods to ensure accuracy and quality.
- Confirmation—Verifying the completion of warehouse activities or transactions.
- Replenishment—Restocking items from reserve storage to picking areas to meet order demands.
- Put-away—Moving received goods from the receiving area to their assigned storage spots.
- Order management—Handling the processes of receiving, processing, and fulfilling customer orders.
- Shipping—All processes related to delivering prepared orders to customers.
- Transport management—Coordinating and tracking the movement of goods into and out of the warehouse.
- Deconsolidation—Breaking down bulk shipments into smaller lots for distribution or storage.
- Relocation—Moving inventory between storage locations within the warehouse.
- Consolidation—Combining multiple shipments or items into a single shipment or location.
- Warehouse structure—Defining the logical layout of a warehouse, including zones and storage types.
- Master data management—Maintaining accurate product, supplier, and customer data.
More advanced warehouse management tasks can include:
- Cross-docking—Directly transferring inbound goods to outbound shipments with minimal storage time.
- Batches—Grouping inventory items by production lot or manufacturing run for tracking and management.
- Kit building—Assembling multiple items into a single package or product bundle for orders.
- Returns—Managing the receipt and processing of goods returned by customers.
- Expiration—Monitoring and managing inventory based on shelf life or expiration dates.
- Cubing—Calculating the volume and space requirements for inventory storage or shipping (using cubic dimensions). Helpful when allocating larger objects to different parts of the warehouse.
- Serial numbers—Tracking individual items using unique identifiers for traceability.
- Weight control—Ensuring that goods meet weight specifications during shipping or storage.
- Customs—Ensuring compliance with regulations for imported or exported goods. This can include printing commercial invoices and packing slips.
- Yard management—Overseeing the movement and storage of trailers and vehicles in the warehouse yard. Only relevant if you have a yard.
- Multi-level storage—Utilizing vertical space with shelves or racks to maximize storage efficiency.
- Multi-warehouse—Managing inventory and operations across multiple warehouse locations.
- Forklift guidance—Using technology to direct forklift operators for efficient material handling.
- Hazardous materials—Safely storing, handling, and documenting dangerous goods in compliance with regulations. Only relevant if you work with such materials.
- Labor management—Scheduling, tracking, and optimizing workforce productivity in the warehouse.
- Scrapping—Disposing of or removing damaged, expired, or obsolete inventory.
- Work orders—Generating and managing instructions for tasks like assembly, repairs, or custom orders.
What Are the Challenges of Warehouse Management?
As mentioned above, warehouse management can include a breadth of tasks, some more complex than others, each with its own challenges. Good warehouse operations ensure customers get what they ordered at the right time, which is vital for customer satisfaction. Effective warehouse management also positively impacts supplier relationships.
Here are the top five warehouse management challenges.
1. Inventory Accuracy
As mentioned at the beginning of this article, inventory accuracy is a big problem for many US companies. When you monitor inventory movements, you can trace the journey they made. Who touched what, who put what where, etc. (More on that below.)
It also means tracking the changing condition of the inventory. For example, if the inventory is expired, damaged, or missing, it should be removed and deducted from your records to keep your inventory accurate.
Not maintaining accurate inventory leads to stockouts, overstocking, and other inefficiencies that can impact customer satisfaction and the efficiency of different operations.
2. Tracking Warehouse Processes and Activity
Businesses must be able to track all warehouse productivity to ensure they are efficient and running without issue. Tracking all processes allows companies to act on inefficiencies early and work on improvements.
This includes monitoring inventory and employee movements. With this information, businesses can make informed decisions with real-time data. For example, if processes are too slow, a business may decide to hire more employees, or if employees are not processing as many orders as usual, they can investigate why.
Without this visibility, it is impossible to know what’s really happening in the warehouse and stay on top of it.
3. Space Utilization and Inventory Organization
An efficient warehouse layout must consider which SKUs are held in which part of the warehouse so that employees know where to go when fulfilling orders or putting away inventory.
A good warehouse layout should be logical, group similar SKUs together, and use naming conventions to help workers find what they need. It should not hinder work. It also must consider how equipment, such as pallet jacks and forklifts, moves through the warehouse.
When space is poorly utilized, it can be a safety risk, prevent staff from accessing or finding stock, lead to damaged or lost inventory, and warehouse processes can take longer to complete. Furthermore, you may be missing an opportunity to stock more products.
4. Technology Integration
Though technology plays a significant role in improving warehouse management, ensuring that the systems you want to use integrate smoothly can be a hassle. Many businesses use multiple systems built by different companies to cover various parts of their processes. Some are not intended to integrate with other systems or have particular requirements.
Poor integration can lead to inventory discrepancies, unnecessary manual work, and other technical problems.
5. Reacting to Changing Circumstances
Situations can change rapidly in a busy warehouse. They can be caused by vendor delays, damaged goods, or even warehouse accidents. When these scenarios occur, warehouse managers must react quickly to ensure minimal disruption to the workload and on-time shipment of orders.
How to Improve Warehouse Management?
‘Warehouse optimization’ is the exercise of improving warehouse processes and reducing the burden of the abovementioned challenges.
Firstly, you can’t improve the warehouse without establishing ways to measure the performance of your operations. This requires setting useful metrics and KPIs to indicate whether the work is progressing as smoothly as expected. To do this, you need reporting tools.
Following on from the point above, you need to regularly inspect these metrics and KPIs, and what is happening on the warehouse floor, to ensure that work is getting done efficiently.
It is also crucial to automate as much of the workload as possible. In ecommerce, automation is vital to remaining competitive, and warehouse management is no different. Identify warehouse processes that are ripe for automation throughout the warehouse.
Typically, manual processes, processes involving multiple people or tools, processes where information is moved from one place to another, or actions following another process are ideal for automation.
In addition, ensuring employee safety is a big part of warehouse management. The warehouse manager is responsible for employee safety, and injured employees can’t work.
Proper warehouse management also must follow a fulfillment strategy. Here are some of the most common:
- Batch picking—Increases picking efficiency by collecting multiple orders simultaneously to minimize travel through the warehouse.
- Region picking—Workers only pick orders in their assigned warehouse regions.
- FIFO (First In, First Out)—The oldest inventory is used to fulfill orders before more recently received inventory.
- LIFO (Last In, First Out)—This is the opposite of the above. The most recently received inventory is shipped before the older inventory (good to use if you don’t have expiration concerns).
- FEFO (First Expired, First Out)—Prioritizes inventory with the closest expiration dates to reduce waste and keep products fresh.
If there are too many warehouse tasks to manage, it might be an option to outsource some or all of them to a 3PL (third-party logistics) service. However, if you keep warehousing in-house, the best way to improve warehouse management is with integrated software and hardware solutions, most notably with a warehouse management system (WMS).
That said, a WMS is just the tip of the iceberg. Taking things a step further, more advanced warehouse management solutions include WES (warehouse execution system) and WCS (warehouse control system) features (we’ll get to those shortly).
What Does a Warehouse Management System (WMS) Do?
Essentially, a warehouse management system is software that simplifies and enhances warehouse operations, from inventory tracking to order fulfillment and all tasks in between. However, like warehouse management, warehouse management software does not have a clear definition, and it can offer various features depending on the type of user it targets.
Many ecommerce companies rely on a WMS to keep their warehouses in order and enhance their workflows. Without a WMS, their business would fall apart.
WMSs have enormous benefits. The most significant is that they eliminate manual processes and guesswork, which reduces human error and speeds up processes. This directly improves customer satisfaction because customers are more likely to receive their orders correctly and promptly, which is vital for your brand’s reputation.
Adopting a WMS also improves employee morale by making tasks easier and more organized. It also means employees can work more confidently, knowing errors are less likely to occur. It also makes onboarding new employees significantly easier.
Furthermore, as employee efficiency increases, you can reduce your labor spend as employees will not have to work as many hours.
A WMS gives warehouse managers a more accurate viewpoint of what’s happening and prevents errors. They can track employee movements, orders, and items around the warehouse. This means that when mistakes happen, it is much easier to trace what happened, fix the issue, and identify why it happened. Traceability is also vital if there is a recall, as the WMS can trace all related items back through the warehouse and all the movements they made.
Lastly, a WMS can help businesses better forecast demand and organize perishable inventory so that employees can pick the right items.
What Should You Look for in Warehouse Management System Software (WMS)?
The checklist of what to look for in a WMS is ever-growing, and unsurprisingly, not all WMS solutions are equally effective. Aside from the functions and benefits listed above (all of which are an absolute must), there are some key things to look out for when shopping for a WMS.
A good WMS should provide clear, easy-to-understand, real-time reporting. This way, you can quickly act on whatever needs your attention in the warehouse and prevent problems from creeping up on you.
The ability to share data with the rest of your ecommerce solution should not be underemphasized. For example, connecting your WMS with your shipping software will make preparing items for shipping enormously easier. The same can be said for inventory and cataloging software.
Additionally, in the last decade, it has become increasingly important to ecommerce sellers that their WMS either integrates with or has built-in WES, WCS, and WFM software. Let’s look at these solutions and what processes they handle.
What Is WES (Warehouse Execution System)?
A warehouse execution system executes various automations and processes by ingesting information from the WMS. A WES should help orchestrate tasks for employees, and find the most optimal way for them to handle the workload, and waste minimal time. It also synchronizes these processes and provides real-time visibility of warehouse activities.
WES is sometimes considered the glue between WMS and other warehouse functions, as it takes information from the WMS and turns it into actions. Using a WES in the warehouse is becoming increasingly crucial for ecommerce sellers. According to research from Global Market Insights, the WES market was valued at $1.7 billion in 2023 and is estimated to grow to $5.2 billion by 2032.
What Is WCS (Warehouse Control System)?
While a WES executes processes, a warehouse control system is the solution that communicates with the hardware. A WCS works with MHE (Material Handling Equipment), warehouse machinery, and smaller devices, such as barcode scanners and mobile devices.
A WMS without a WCS cannot communicate with any devices and machinery in your warehouse, meaning important information cannot be sent while on the warehouse floor or actions automated.
The demand for WCS is expected to grow exponentially in the coming years. Next Move Strategy Consulting estimates that the WCS market was valued at $3.55 billion in 2023 and will be worth $10.12 billion by 2030.
What Is WFM (Workforce Management)?
WFM enables businesses to designate roles for employees who handle specific processes, such as pickers, shippers, and receivers. A WFM can provide or limit access to certain parts of the WMS or tasks, such as the ability to pick certain high-value or hazardous items.
Access to administrative features can also be limited. For example, managers can access the entire system, while shippers may only need access to the shipping functions. Shift management can also be a feature of WFM systems, allowing warehouse managers to schedule shifts and employees to clock in and out.
What Is The Future of Warehouse Management Software?
In the future, different warehouse software solutions—WMS, WCS, WES, and WFM—will work more fluidly with each other, add more features and integrations, improve integration, and offer more customization.
Further ahead, AI (Artificial Intelligence), IoT (the Internet of Things), and AR (Augmented Reality) may play a bigger role in warehouse management systems as solutions strive for further efficiency.
Though this may seem a long way away, the point remains that a good WMS continually develops and improves, adding new, valuable features and ensuring that you won’t get left behind as technology changes.
Why Is Skustack the Best WMS?
Skustack stands out as the best WMS for a plethora of reasons. In addition to the ‘basic’ functionality listed above, Skustack also has ‘advanced’ functionalities that may not be available in standard WMS systems.
Not only does it excel at warehouse management, but as part of the Descartes ecosystem, Skustack works with shipping software Shipbridge and Descartes Sellercloud for inventory, order, and catalog management, as well as other Descartes products.
Plus, its real-time synchronization with Descartes Sellercloud provides instantaneous updates to your source of truth and the channels it connects with. For example, if an order is canceled, Skustack will know that far faster than any other WMS out there, without any human having to manually update the system.
Skustack’s mobile applications (Android and iOS) can also be installed on devices and connect to the WMS, enabling employees to scan products, receive orders, pick products, and more on the go.
Equipped with the Skustack app, employees can reduce travel time and receive instant confirmation that a task has been successfully completed, eliminating guesswork. Employees can even filter picklists by warehouse region to enhance their workflow.
Skustack Lens, Skustack’s warehouse visualization tool, allows businesses to track inventory and employees in real time and can help you design and improve the layout of your warehouse. Furthermore, Skustack Lens’s workforce management features can help you monitor employee task duration in real time and track employee time logs with customizable time stamps.
Lastly, Skustack is constantly improving with new features, covering more use cases, and improving how ecommerce sellers handle their warehouse operations, whatever part of the process they belong to. Skustack updates are posted frequently here.
However, that’s just the beginning. Skustack has already helped hundreds of ecommerce businesses improve warehouse efficiency. Discover their stories here.
Book a Skustack demo today.
Key Points
You’re now a pro in warehouse management. Remember these key points.
- Warehouse management involves everything related to a warehouse in an ecommerce business, including monitoring, organizing, and improving operations to ensure proper inventory handling.
- The biggest challenges to warehouse management are tracking processes, reacting to changing circumstances, inventory accuracy, space utilization, and technological integration.
- Establishing KPIs and metrics, automating manual tasks, utilizing a fulfillment strategy, and adopting a WMS can improve warehouse management.
- A warehouse management system (WMS) is software businesses use to simplify, enhance, and monitor warehouse operations.
- Skustack offers everything your ecommerce business needs to keep your warehouse efficient and reach its optimal potential.