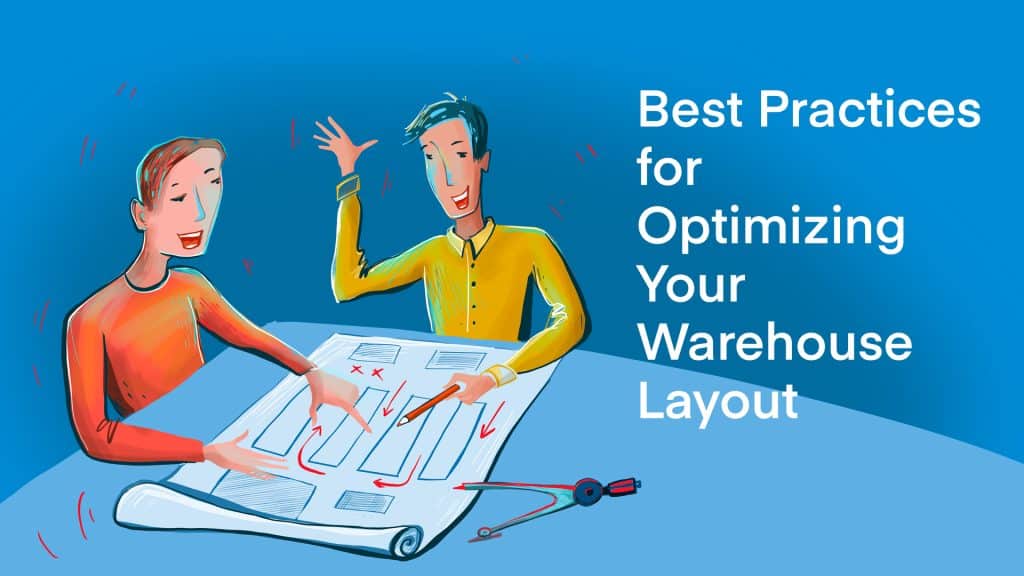
As your ecommerce business scales, so do your needs for warehouse locations to store inventory and fulfill orders. Beyond the physical space, you need a warehousing plan that can expand and adapt. When facing this challenge, it can be tempting to outsource your inventory and fulfillment responsibilities to a third party.
Not so fast.
The reality is that with the proper planning, tools, and WMS (Warehouse Management System), creating and maintaining your warehouse space isn’t as overwhelming as you might assume. Running your own safe, efficient, and optimized warehouse will maximize your profits and put you in charge of further growth.
To start, you need to figure out your ecommerce business needs. The next step is to map out the best use of that space. In doing so, there are several best practices worth considering.
Ecommerce Warehouses Need Dedicated Spaces for Dedicated Purposes
Instead of looking at your new warehouse as a daunting blank canvas, break down the space into regions and critical locations. Focus on compartmentalizing inventory management and fulfillment responsibilities into designated areas.
Reception
You need a dedicated space to receive incoming supplies and transition them into your inventory. This means space to sort, catalog, and scan the merchandise before moving it to the appropriate storage area.
Depending on what you are selling, this could require anything from rows of sorting bins to pallet landing spots. Whatever your storage and organizational needs are in this space, your receiving area must function accurately to ensure your newest inventory is correctly accounted for. Reception must also work quickly to avoid logjams at your receiving dock.
Skustack, Descartes Sellercloud’s patented warehouse management platform, has been designed from the ground up to create and maintain accurate inventory records for every piece of merchandise that enters your possession.
Whatever your storage and organizational needs are in this space, your receiving area must function accurately to ensure your newest inventory is properly accounted for. Reception must also work quickly to avoid logjams at your receiving dock.
Inventory Storage
The most significant footprint of any region of your warehouse will likely be your storage area. This combination of bins, racks, and stacks must be organized and optimized so that products can be quickly sorted and stored while simultaneously being picked for outgoing orders.
Laying out the storage section of your warehouse can be a puzzle in and of itself. Typically, your highest volume SKUs should be most easily accessible to the other areas of your warehouse. Conversely, your seasonal and overstock merchandise can be tucked farther back off the main pick path. Other considerations, such as product variations, inventory sizes, and forklift accessibility, may also determine what goes where.
An optimized storage plan allows your sorting and picking teams to get what they need quickly. Similarly, as customer patterns shift, you should be able to adjust your stock locations accordingly. Flexibility is a critical component of effective warehouse planning.
If properly managed with an effective WMS, a dynamic warehouse will consistently outperform a static one. Working together, Descartes Sellercloud’s robust inventory management tools can provide you with the metrics to recognize these changing patterns, while Skustack can provide the means to adjust stock locations without disorienting your warehouse staff.
In the end, an optimized storage area means a worker can scan a code and know exactly where the item they are looking for is located. From there, the product can be picked and moved through the warehouse workflow to packing and shipping.
Returns
Returned merchandise needs to be processed and handled separately from the new inventory. Furthermore, RMA stock must be dealt with before it becomes a pile of dead stock that can negatively affect customer service metrics. This is an area where Skustack is especially valuable as a WMS tool.
Workers can quickly scan, assess, and process returned shipments and move them along to either be resorted, refurbished, or destroyed. Making space for this workflow in your warehouse design helps maintain prompt and accurate RMA processing as a priority.
Picking and Packing
You will certainly want a specific location for your picking team to procure and organize the goods ready for outbound orders. Doing this on the fly in your warehouse’s storage or shipping areas can quickly lead to issues like gridlock or hazardous clutter. Instead, having a dedicated space for orders to be picked and assembled can keep things running smoothly. Skublox‘s put-to-light pick-to-light system is a useful tool for driving this type of workflow.
Goods can be picked in batches, scanned, and placed into dynamically color-coded slots that show workers what goes where. Once an order is fully sorted, the lights on the picking side go out, and the shipping side can take over pulling and packing for shipment.
Shipping
This department of your warehouse is the end of the road for your outgoing packages. This also means it is your last chance to ensure everything is labeled correctly and loaded onto the appropriate outbound vehicle.
Even if everything has gone perfectly up to this point in the package’s lifecycle, an error here can cost you. Such an important part of the fulfillment workflow requires its own dedicated space. In some cases, packing may be included in this area. In others, it makes more sense to give the packing process its own separate space.
Factors to consider include:
- The quantity of packages you ship.
- The number of different shipping options you offer.
- The variety of products that can be packed into a single order.
The simpler your average order, the more reasonable it may be to include this in your shipping department’s charge. Regardless of your shipping circumstances or the size of your ecommerce business, Shipbridge, Descartes Sellercloud’s included shipping platform, can help keep this aspect of your warehouse running efficiently.
Shipbridge makes it easy to create custom rules based on package characteristics such as shipping provider, destination, package weight, order value, marketplace, and more. No matter how many channels and shipping carriers you partner with, you can ensure the packages are properly labeled and shipped.
When In Doubt, Follow the Physical Flow of Your Inventory
Dedicated spaces for every inventory management process are essential, but so is properly configuring how these dedicated spaces fit into your overall layout.
When arranging your warehouse, putting the puzzle together starts with tracing the life cycle of your SKUs. Do it well, and inventory should enter and exit like a well-oiled machine. Start with your shipping docks—where inventory comes in and where it ultimately goes out.
If your warehouse has the option of separate dock spaces for loading and unloading, that is ideal. You can lay out a path that flows like a river from receiving to storage, picking and sorting, and shipping. It doesn’t matter if your warehouse is shaped like a U, an L, or an I—if you can create a direct path from reception to shipping, do it!
If you are forced to use the same docks for shipping and receiving, recognize that this shared space is a prime bottleneck location. You will need to design warehouse workflows that can account for this circumstance.
The key is to have systems that prioritize keeping that shared dock space as clear as possible. Regardless of your warehouse shape or dock configuration, the tightest loop from receiving to shipping should be reserved for processing the orders for your best-selling merchandise.
Prioritize physical efficiency when settling on your final layout. In all of this, don’t forget about returns. Often, returns get unloaded and relegated to piles off in the corner, quick to be overlooked.
In highly competitive ecommerce marketplaces, processing returns as quickly and efficiently as you do new orders matters. It is key to maintaining your marketplace standing and customer satisfaction ratings.
Have a strong RMA workflow and a designated physical space where it can be regularly carried out. In most cases, returned merchandise will be processed and stored separately from your new stock. As such, opt for a location close to both your receiving area and where this storage will be situated so as not to interfere with your other logistical workflows.
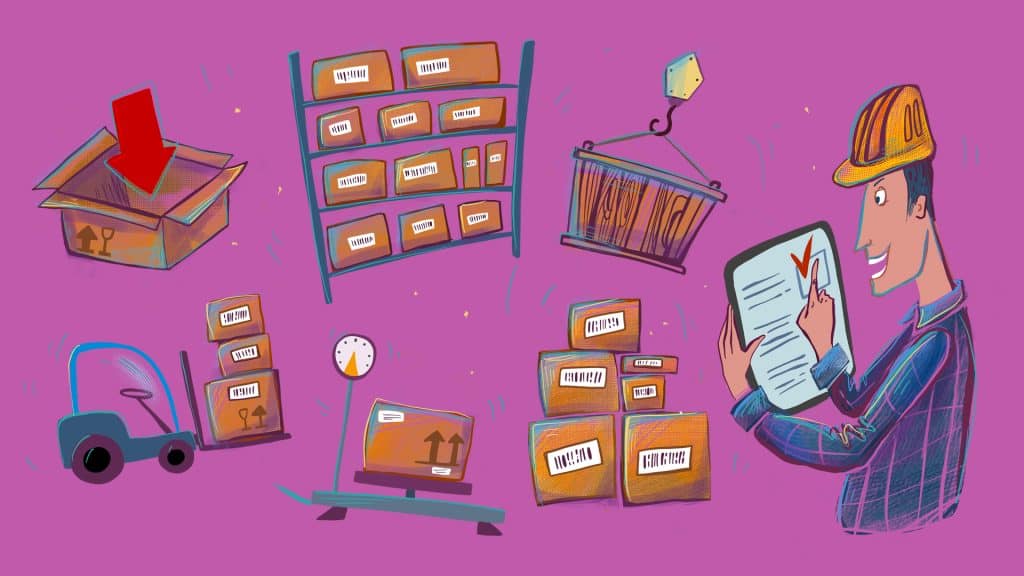
Whole-Warehouse Considerations
Zooming out, there are several general items that you should always keep in mind when optimizing the warehouse’s physical efficiency.
Space
Open space is critical. In the big picture, extra space provides room to grow, giving you the potential to carry additional inventory levels and add additional SKUs to your catalog. At the granular level, however, space means that every person, item, and piece of equipment can easily move through stacks, around bins, and between areas.
Ultimately, space must be planned for in advance to help maintain a smooth physical workflow and promote a safe working environment. Even the most optimized pick path becomes irrelevant if inventory and warehouse workers can’t move through it freely. When aisles and movement areas become cluttered, this may be a sign that you need to reconsider your warehouse layout (or even consider expanding to a larger one).
Lighting
Warehouse lighting matters. Every shelf, bin, packing surface, loading dock, and corner of your warehouse should be brightly lit. Not only does this make it easy for your warehouse team to find items and correctly process orders, but it also reduces the likelihood of on-the-job accidents. Properly positioned LED lighting can illuminate every corner of your warehouse and help keep operating costs down compared to traditional fluorescents or halogens.
Technological Integrations
Plan ahead for technology integration—it becomes infinitely more challenging if left to the last minute. When designing your warehouse spaces, account for the power, networking, and charging needs of the tech tools you will use. Identify convenient and secure locations for your critical tech so it is always within reach and ready to go when your workers need it.
Training
Training your staff on warehouse protocols and procedures is essential. Even a perfectly designed warehouse system is pointless if it lacks the team to execute it. Moreover, there are safety and security concerns that you must be proactive about. This can be a time-consuming process, but it is unavoidable.
That is why we have designed the Descartes Sellercloud platform and technologies to be as intuitive and user-friendly as possible. Skustack’s Android-based scanning interfaces make onboarding new employees easier by design. Similarly, Skublox’s put- and pick-to-light system keeps accurate order processing simple and streamlined, while Shipbridge takes the guesswork out of matching the right shipping labels to the right packages.
In each of these cases, our technological tools allow your warehouse and staffing to scale easily while keeping training hours to a minimum.
Want to see how Descartes Sellercloud and its modules can help you optimize your ecommerce warehouse? Contact us directly for a free demo and consultation.