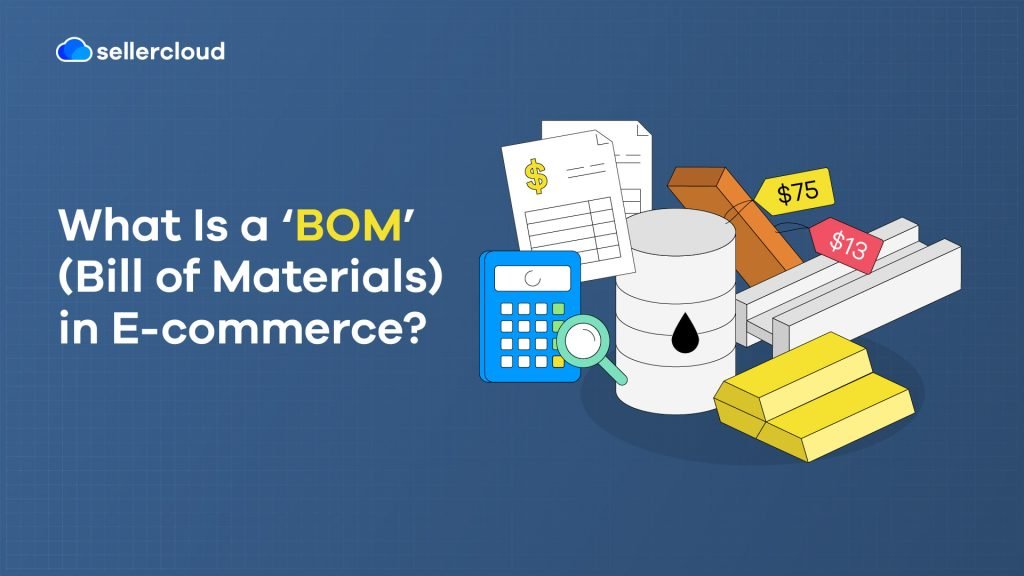
- BOM stands for ‘Bill of Materials,’ and though the term originates from the manufacturing industry, in ecommerce, it is a helpful way to construct products and kits before sale.
- With Descartes Sellercloud, ecommerce sellers can create kits with different rules based on the importance of the components.
Suppose you sell products with different components and parts that must be constructed before sale. In that case, BOMs are an excellent way to organize them, particularly if there are different product variations or if the product can be customized.
Furthermore, many ecommerce businesses rely on kitting or bundling products under one SKU to lure in new customers looking for deals, appeal to returning customers, and increase order size and value. BOMs are an ideal way to organize this, too. So, how do you keep up with all the different components and parts and ensure they’re always in stock? How do you prevent the costs from getting out of hand?
In this article, we’ll explain what BOM is in ecommerce, what it consists of, why they are useful, how to construct one, and some best practices to follow.
Note: We’re focusing on BOM in ecommerce, not manufacturing or engineering, though we will touch on these areas as they have influenced how we organize BOMs.
What Does ‘Bill of Materials’ (BOM) Mean?
A bill of materials can be considered a list of parts required to construct something, such as a product. However, a bill of materials is much more than a list. It can be compared to the instructions to build something from IKEA, and shows you how to assemble it. A BOM breaks down all the details and requirements for each part, which helps with inventory management, purchasing and ordering, delivery processing times, and cost management.
Is COGS (Cost Of Goods Sold) the Same as BOM?
No, COGS and BOM are not the same. COGS stands for ‘Cost Of Goods Sold.’ It is a financial metric representing the direct costs of producing goods or services. COGS doesn’t explain how a product or kit should be constructed or list its details. It focuses solely on the costs of producing goods and delivering them to the customer.
What’s the Difference between a Bill of Materials (BOM) and a Bill of Quantities (BOQ)?
Bill of materials (BOM) and bill of quantities (BOQ) are similar in name and purpose. However, while both are documents used to list and quantify materials, BOM is used for assembling products, while the construction industry uses BOQ.
BOQ factors in the labor requirements because these are needed for construction. BOM does not include any labor requirements. Furthermore, BOM lists ‘subassemblies,’ which are the components and parts needed to finish a product or kit, and can drill down into their details. A BOQ does not contain subassemblies.
What Are Other Names for Bill of Materials (BOM)?
Bill of materials can go by many names, some of which you may have already come across outside the ecommerce industry. Some include:
- Assembly component list.
- Associated list.
- Product structure.
- Production recipe.
The name you use can depend on the industry you work in. In ecommerce, you may refer to a BOM when assembling a product or kit, or use another term. BOMs are particularly useful when creating custom-ordered products from which you must source and prepare materials.
Why Is a Bill of Materials (BOM) Important?
A bill of materials is important for several reasons. Firstly, it ensures the necessary components are available for assembly, keeping the process efficient and avoiding delays. It also informs warehouse pickers which components to collect, differentiating them from others, and informs you when a kit is unavailable because of missing components.
A BOM also helps estimate the costs of the components needed and plan purchases, so you can manage and track your inventory and avoid overstocking and understocking. On top of that, BOMs are also useful for identifying potential product vulnerabilities, most commonly if a component or part is challenging to get hold of. Knowing what you need in advance helps avoid shortages or supply chain disruptions.
Lastly, because BOMs keep you organized and efficient, this helps reduce waste.
What Does a Bill of Materials (BOM) Include?
What might be included in a BOM can depend on your industry and the product you are putting together. Here’s a quick list of what’s commonly included:
- Part name—What is the name of the component or part? Alternatively, you may use the component’s SKU.
- Part number—Often an alphanumeric code that refers to the component or part’s details in shorthand. Some companies may use the component’s MPN (Manufacturer Part Number) instead of a part number.
- Quantity—How many do you need? Some products may need multiple parts for subassemblies. For example, a wheelbarrow will require a frame (subassembly), and the frame will require several screws.
- Unit of measurement—Often, it can be the number of components needed, but it could be inches, centimeters, ounces, etc. The units used should be consistent with similar parts. On a BOM, a unit of measurement may just be written as ‘Unit.’ When the unit of measurement is just one item, it can be written as ‘each.’
- Part descriptions—Descriptions are important because they can help the user of the BOM differentiate between similar parts, colors, and dimensions, for example.
- Unit cost—The cost per unit required.
- Cost—Unit cost multiplied by the number of units.
- Additional notes—Comments and notes may include images and diagrams, documents, and instructions to construct the product.
It’s worth mentioning that a BOM should also include consumables, such as glue, wire, and fasteners, or anything else used to construct or package goods.
A BOM may also include:
- Manufacturer’s name—This is useful when sourcing components and parts, as users know where to acquire them.
- Alternate parts—Parts or ‘alternative SKUs’ that can be used instead when unavailable.
- Priority analysis—Which parts are most critical? This helps the user prioritize which parts to purchase first. Priority could depend on the cost or lead time.
- Procurement specification—Describes how components are procured. Typically, ‘P’ stands for Purchase, ‘M’ for Modified, and ‘C’ for Custom.
The columns in your BOM can be simple if no complex construction is required.
What Does a Bill of Materials (BOM) Not Include?
While a BOM can act as a comprehensive list and instructions for constructing a kit, several things are not included. These are:
- Labor costs—Someone will need to assemble the product. However, the labor and the related costs are not included in a BOM.
- Delivery costs—Anything to do with delivering orders to customers is not included.
- Holding/carrying costs—BOMs do not consider any costs you may incur by holding inventory.
- Inventory shrinkage—Any costs incurred from missing, stolen, broken, or expired inventory (though a BOM may contain information on alternative components that can be used).
- Marketing and advertising costs—BOMs do not outline how to market or advertise a product, nor list any associated costs.
- Any sales or administrative costs associated with selling a kit—These are costs of doing business and are not included in constructing a product or kit.
In ecommerce, BOM strictly includes the costs of the components and parts needed for a product or kit.
What Are the Impacts of Having More or Less Levels in the Bill of Material (BOM)?
BOMs are hierarchical and often come in two formats—‘single-level’ and ‘multi-level’ (also called an ‘indented BOM’). For both single-level and multi-level BOMs, the top level is the finished product or kit, and the next level is called the subassembly, which is the components or other products required for a kit.
In a multi-level BOM, there is an additional level below the subassembly/components for any parts they may need in their construction. Single-level BOMs are simpler than multi-level BOMs because they do not have parts, which means less work is required to assemble their components.
The more levels your BOM has, the more complex it becomes. This is because each component and its parts have all the columns of information mentioned above.
What Are the Different Types of Bills of Materials (BOM)?
Though the term BOM originates from manufacturing because it’s so useful, its usage has spread to other industries as a helpful way to break down the requirements for putting something together. Depending on your industry, you may have heard of variations of BOM. Here are some of the most common:
- MBOM—‘Manufacturing bill of materials,’ used in manufacturing.
- EBOM—‘Engineering bill of materials,’ used in engineering.
- SBOM—Can stand for ‘Sales Bill of Materials’ or ‘Software Bill of Materials.’
However, in ecommerce, you will likely not need to worry about these variations, though it may be helpful to know that other industries use them.
How Do I Make a Bill of Materials (BOM)?
How you create a BOM will vary depending on the complexity of the product or kit. A simple single-level BOM will have fewer levels, while a more complex multi-level BOM will have more.
To create a BOM, start by listing everything you need to produce your product or kit, and then source all the information about each item and list these details (check ‘What Does a Bill of Materials (BOM) Include?’ above for the different details you will need). You can also create a diagram to map the components to better understand how they fit together, the number of each required, and anything else a user may need to know.
When considering what information to include and how to put the product or kit together, consider who will construct the BOM and their knowledge level. Don’t include things they don’t need to know because this can be confusing and will waste the user’s time. Focus solely on what the user needs to complete the BOM.
Furthermore, BOM lists can be displayed in different formats. It’s best to use a template that works for you, though this might be dictated by the type of product you are putting together. When you have amassed all the information you need, ensure the levels are properly indicated, and remember to organize them according to what they relate to. For example, parts should only be listed under the components they are needed.
A common way of doing this is with numbers.
- 1—Signifies the top level (AKA, the finished product or kit).
- 2—Signifies the components (which may be referred to as ‘subassemblies’).
- 3—Signifies the parts that make up the components (if it is a multi-level BOM).
Some BOMs break things down into lower levels than just these three. Alternatively, you can indent the subassemblies and parts or use both numbering and an indent to better clarify the different BOM levels.
What Are the 5 Best Practices When Working with BOMs?
There are plenty of things you can do to keep your BOM as practical and useful as possible. Here are the top five best practices for BOMs:
1. Use Standardized Templates
Companies may use BOM templates to make BOMs easier to make. Whoever needs to fill it out shouldn’t need to start all over again every time. A standardized structure also speeds up the process as the user knows what to look for. Furthermore, it reduces errors and the chance of missing information.
2. Keep Units of Measurement Consistent
Ideally, if one component is measured in inches, you shouldn’t measure another in centimeters, as this may cause confusion and mistakes.
3. Keep Naming Conventions Consistent
Just like unit measurements, your naming conventions should also be consistent. Users should easily understand what is required of them when they see the different columns and components, and any notes detailing how the different parts come together.
4. Cut Any Unnecessary Information
On review, are any of the details you’ve included not needed? Will they only serve to confuse the reader? If so, they don’t belong on a BOM. Remember that a BOM should help the user put a product together, and anything else is additional baggage that’s not needed.
5. Use Software to Create and Manage BOMs
Software makes working with BOMs easier. It enables ecommerce sellers to oversee and track their inventory and set up what defines a kit from a central interface. For example, you can see how many kits you can make based on your inventory and configure rules accordingly. More importantly, software enables sellers to automate and reduce manual actions, saving time, increasing efficiency, and preventing mistakes.
How Can Descartes Sellercloud Help Ecommerce Businesses with Bills of Materials (BOM)?
As mentioned above, using a software solution to manage your BOMs for products and kits makes the process more efficient in multiple ways. Descartes Sellercloud enables sellers to do this with its flexible and highly functional inventory and listing features, designed according to seller feedback.
By keeping your inventory and listing details connected in one place, you can track component quantities and have a calculated kit quantity based on the available components, so you always have enough to fulfill orders and prevent costs from spiraling.
Using Descartes Sellercloud’s kit assembly feature, sellers can organize products and kits that must be assembled and track the raw materials required at a component level. For example, an ecommerce seller selling custom carpets could use Descartes Sellercloud’s kitting functionality as a BOM to list and track all the necessary components, calculate the total cost, manage it as a single product, and assemble it on demand.
You can configure kits in three ways with Descartes Sellercloud:
- All component kit—Only available when all components are available. If just one component is out of stock, the kit will also be considered out of stock.
- Main component kit—Allows you to choose the main component of your kit. When this component is unavailable, the entire kit is unavailable.
- Independent kit—Kits are separate from the rest of your inventory, so the number of kits and the components do not impact one another.
Configuring kits empowers sellers to work with components in a way that works for their business. You can also receive reports on kit performance.
Curious how Descartes Sellercloud helps ecommerce businesses with kitting? Watch P3 Global’s testimonial on how Descartes Sellercloud helped them.
Want to find out how Descartes Sellercloud can help your business succeed? Book a demo today to find out.
Key Points
You now know all there is to know about bills of materials. Keep in mind these key points.
- BOM stands for ‘Bill of Materials.’ A BOM is used to detail how a product should be assembled. In ecommerce, a BOM can also show how a kit should be constructed.
- BOM is different from COGS and BOQ. COGS is used to calculate the costs of producing and shipping goods, and while BOQ is similar to BOM, it is used in the construction industry and includes labor costs.
- BOMs help companies calculate the costs of the components and parts they need for a product, manage their inventory, and keep their operations efficient.
- To create a BOM, you need to list all the components and parts needed to create a product or kit, including the relevant details for construction, and order them appropriately.
- Descartes Sellercloud empowers ecommerce sellers to configure different kitting rules to make constructing BOMs easier, faster, and more efficient, reduce mistakes, and work how they need to.