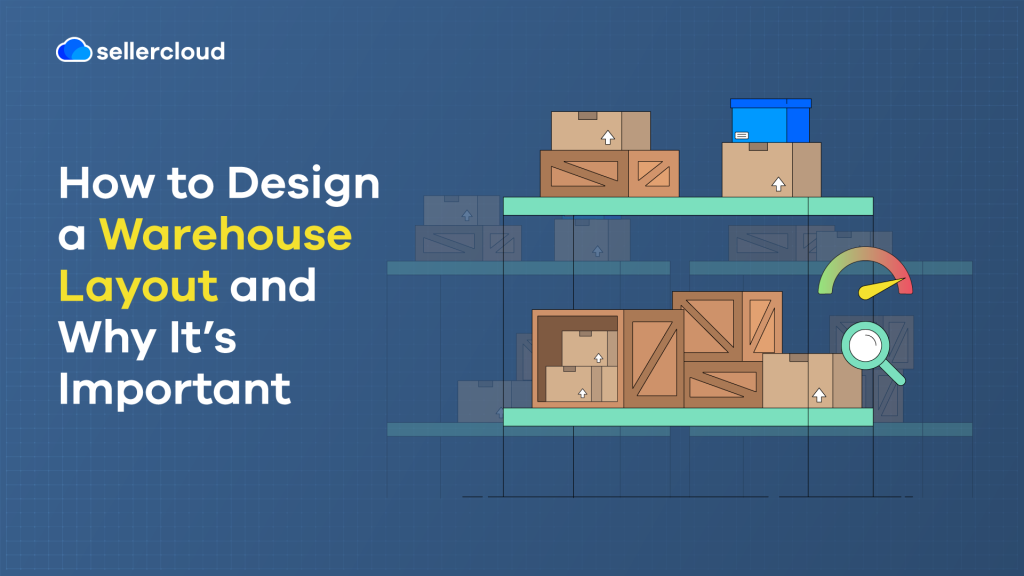
- A poor warehouse design can later impact many areas of your business, but you can optimize your layout in many practical ways.
- Skustack and Skustack Lens help monitor how inventory and staff move through warehouses, helping merchants optimize warehouse layouts.
According to data from Statista, in 2020, there were approximately 151,000 warehouses globally, of which 25,500 were located in North America. More importantly, though, due to the ecommerce boom, the number of global warehouses is predicted to reach 180,000 by 2025. So warehouse storage needs are increasing significantly, which is all the more reason to make your warehouse as efficient as possible.
A poorly designed warehouse layout can cause many problems, and a well-designed layout can solve many. Plus, if you don’t optimize your warehouse layout, it could harm your business in more ways than further down the line.
This article will explain why warehouse layout is important, what affects warehouse layout, and how to design and optimize your warehouse layout.
Are you planning to relocate your warehouse? Then you might need our Guide to Moving Warehouses!
Why Is the Layout of Warehouses Important?
Your business’s warehouse layout impacts various aspects of your operations and can substantially impact your overall efficiency and success.
Firstly, a well-designed warehouse layout allows for efficient space utilization. According to some estimates, 59% of warehouses utilize up to 90% of their space. Maximizing available warehouse space allows you to store more inventory without costly expansions. This saves you money, ensures that your inventory is well-organized and easily accessible when needed, and enables you to sell more products without needing more warehouse space.
Secondly, an optimized warehouse layout enhances your business’s productivity by improving the flow of products and staff through your warehouse. Doing this minimizes unnecessary movement and reduces the time it takes to complete tasks. This means faster order processing and increased productivity, ultimately helping you meet customer demands more efficiently.
Another benefit is that you can reduce errors. A logical and well-organized layout minimizes errors in inventory management. Proper organization of storage locations (as well as clear labeling) makes it easier for employees to locate and retrieve the right items, thus reducing picking errors and improving overall order accuracy.
Furthermore, an efficient warehouse layout creates a logical sequence of activities from receiving to storage, picking, packing, and shipping. By streamlining the movement of goods, you can ensure a smooth workflow that saves time and keeps your operations running efficiently.
Lastly, the layout of your warehouse impacts employee safety and satisfaction. A well-planned layout considers safety considerations, such as clear aisles, designated walkways, and proper lighting. A safe and comfortable working environment can also promote employee satisfaction and reduce the risk of accidents or injuries.
What Are the Effects of Poor Warehouse Layout?
One of the most obvious consequences of a poorly planned warehouse layout is inefficient space utilization. If you plan your warehouse poorly, you risk wasting valuable space, encountering overcrowded areas, and having difficulty locating and accessing inventory. This limits your storage capacity and hampers your ability to accommodate growing inventory demands.
In addition, a disorganized warehouse layout disrupts the workflow and reduces productivity. Employees may spend excessive time searching for items, navigating through cluttered areas, or dealing with bottlenecks. This results in longer order processing times and potential customer dissatisfaction.
Poor organization and unclear labeling contribute to increased errors and delays. Employees may struggle to find the right items, leading to incorrect shipments, order mix-ups, or delays in fulfilling customer orders. Such mistakes can harm your reputation and strain customer relationships.
Moreover, a chaotic warehouse layout poses safety hazards. Blocked aisles, cluttered pathways, or inadequate lighting can increase the risk of accidents, injuries, and potential liability issues. Neglecting safety endangers employees and negatively affects morale and job satisfaction.
A poorly designed warehouse layout also creates inefficiencies in material handling. Improperly positioned storage areas or unclear pathways hinder the smooth movement of goods. This results in additional handling time, increased equipment wear and tear, and potential inventory damage.
What Affects Warehouse Layout? 10 Factors to Consider When Designing a Warehouse Layout
Check off this list before taking your pen to paper to design your perfect warehouse layout.
1. Your Storage Needs
A warehouse is useless if it doesn’t cover your basic storage requirements. Your storage needs must consider the size of your products and how quickly they leave the shelves. This means calculating your sales velocity.
2. Keeping Your Workflow Optimized
Always think of the journey your staff takes from receiving an order to finding and picking it, preparing it to be shipped, and sending it out—how can you make that journey smoother? Any new warehouse layout shouldn’t make the journey longer or more complicated.
3. Keeping Your Staff Safe
Highly important and an absolute must—your warehouse must keep your employees safe at all times! According to an article by The Law Office of Matthew E. Russell, the seven most common warehouse injuries are:
- Forklift accidents.
- Hit by an object.
- Caught between objects.
- Slips, trips, and falls.
- Hazardous materials.
- Overexertion injuries
- Repetitive stress injuries
So, if possible, ensure you can design your layout to reduce the chances of these kinds of injuries in your warehouse.
4. Complying with Regulations
Your warehouse layout must adhere to relevant regulations and compliance requirements. Make sure you understand which regulations apply to your workplace. Research fire safety codes, hazardous material storage guidelines, and any industry-specific regulations that apply to your operations. You can check out OSHA’s documentation on warehouse safety here.
5. How to Scale Out for the Future
You want your business to grow, right? Of course you do. However, it can be hard to expand without the proper warehouse space. Ensure your warehouse layout is scalable to plan for future growth and changes in demand. Consider flexible storage options and the ability to reconfigure the layout as your business evolves.
Forecast your potential future capacity—but to do that, you first need to know your current capacity. Be warned: Don’t invest in something too large, as it could cost you a lot in the future.
6. Keeping Your Warehouse Accessible
Create a layout that allows easy access to all warehouse areas. Ensure that aisles and pathways are wide enough to accommodate equipment and allow for the efficient movement of goods. Furthermore, on a practical level, how will your employees pick products? Keeping products in easy reach will speed up picking and keep employees safe.
7. How Products Will Flow Through Your Warehouse
Do you know how products move through your warehouse from point A to point B? Ensure your new warehouse layout minimizes the distance employees need to travel when handling products, whatever the task—receiving to storage, picking, and shipping. Ideally, you’ll want as few steps as possible to complete each task.
8. Investing in the Right Tech for Your Warehouse Needs
Large companies with complex and fast-moving operations can greatly benefit from tech like Skustack and Skustack Lens to keep their operations efficient. It’s important to reserve space for this tech in such companies. This includes considering space for automated systems, conveyor belts, barcode scanners, and other technologies that can enhance efficiency and accuracy.
According to estimates by McKinsey, “between 400 million and 800 million individuals could be displaced by automation and need to find new jobs by 2030.” So, merchants must consider this when designing future-proof warehouses.
9. How Your Layout Could Impact Order Fulfillment
Try to optimize your warehouse layout to support efficient order fulfillment processes. Consider order picking, packing, and shipping and the spacing these tasks require to minimize travel time and streamline the fulfillment process.
10. Keeping Your Eyes Open for Cross-Docking Opportunities
If applicable to your business, evaluate the potential for cross-docking. You can consider designing the layout to facilitate the direct transfer of goods from inbound to outbound areas, reducing the need for storage and handling.
What Are the Different Types of Warehouse Design?
The four most common types of warehouse layout design are:
- U-shaped.
- L-shaped.
- I-shaped.
- Fishbone.
We will examine them in greater detail below, but please note that not all warehouses follow these layouts. Some older warehouses or repurposed warehouse spaces may have less conventional layouts. Likewise, warehouses are built for various other purposes, each with pros and cons.
What Is a U-Shaped Warehouse Layout?
A U-shaped warehouse layout features a central area with storage and work zones arranged in a U shape. This design promotes efficient material flow, reduces travel distance, and allows clear visibility and accessibility throughout the warehouse.
What Is an L-Shaped Warehouse Layout?
An L-shaped warehouse layout has two perpendicular sections that form an L shape. This design is suitable for maximizing space in corner areas. It provides flexibility in organizing storage zones and allows for efficient workflow by separating different functional areas within the warehouse.
What Is an I-Shaped Warehouse Layout?
In an I-shaped warehouse layout, storage and work zones are organized in a straight line. This straightforward design optimizes the use of space, promotes easy navigation, and facilitates a linear flow of operations from receiving to shipping. I-shaped warehouse layouts can also be called ‘straight-line flow’ or ‘through-flow.’
What Is a Fishbone Warehouse Layout?
Also known as a ‘spine’ or ‘backbone’ layout, a fishbone layout features a central aisle with storage areas that branch off like the bones of a fish.
This layout allows for efficient use of space and promotes clear organization and accessibility of inventory and equipment.
How to Layout Warehouse Racking?
As with planning any element of your warehouse, your business’s needs come first. Warehouse racking should be determined by the types of products you sell, particularly size and any special storage requirements.
Knowing this will help you select the most suitable racking systems. The three most common types of racking systems are:
- Selective racks—Individual pallets accessible from the aisle (most common).
- Drive-in racks—Pallets stored in a single row, accessible from one side for last-in, first-out (LIFO) inventory management.
- Push-back racks—Pallets stored on inclined rails allow for multiple depths and automatically push forward the next pallet when one is retrieved.
Your warehouse’s racking must also leave enough space for maneuverable aisles for your equipment and other machinery, like forklifts, to navigate the space safely and comfortably.
It is also wise to utilize as much vertical space as possible by installing tall racking systems or incorporating mezzanine floors. This is one of the best ways to maximize storage capacity. However, maximizing racking capacity should be balanced with accessibility—there’s no point in having racks all the way to the ceiling if staff cannot reach them.
To circumvent this, position frequently picked items in easily accessible areas to minimize retrieval time and place low-demand items in less accessible locations to optimize overall space utilization. Your company’s most popular SKUs should always be the most accessible—either low down or strategically located a short distance from your dedicated sorting and shipping space to improve efficiency.
Finally, use clear and consistent labeling for racks and storage locations. Proper labeling enhances accuracy and efficiency during item retrieval.
How Do You Separate Warehouse Space?
When deciding how to separate warehouse space, start by defining zones by the activities that should take place, such as receiving, storage, picking, packing, and shipping. Additionally, don’t forget to designate areas for equipment storage and maintenance to ensure they are easily accessible.
Doing this leaves you with all the remaining space you can use for your inventory, which you should then divide into smaller areas based on the product categories you stock. One way to clarify the distinction between the different product types is by installing physical barriers like walls, partitions, or fencing to create clear boundaries.
This can accompany signage and floor markings to indicate racks, aisles, and other areas within the warehouse. This enables employees to easily identify different zones and follow designated pathways. As mentioned above, organizing inventory vertically with racks is one of the best ways to utilize warehouse space and easily separate different product types.
Ensure your plan to divide up space in the warehouse is followed and doesn’t begin to fall apart—that could be a sign that it doesn’t work.
How Do I Optimize My Warehouse Layout?
For those who already have a warehouse in use and are thinking of making improvements, there are always plenty of things you can change. The first thing you should do is get feedback from the people who use your warehouse daily. If you’re not on the warehouse floor day in and day out, there are many small things you could be missing.
Though some of the issues your staff report may seem minor initially, they could snowball into major issues if they occur frequently and affect staff efficiency. Once you know the issues you are trying to resolve, you can think about reorganizing your current warehouse layout. Top things to consider when optimizing your warehouse layout:
- Group frequently accessed items near the shipping or packing area for easy retrieval and place slower-moving inventory in less accessible areas.
- Consider utilizing vertical storage options such as mezzanine floors, vertical racks, or multi-level shelving. This helps maximize storage capacity without expanding outward.
- Aim to minimize unnecessary movement and ensure a logical flow from receiving to storage, picking, and shipping.
- Explore warehouse management systems (WMS), barcode scanning, or automated inventory tracking systems to streamline processes and improve accuracy.
Once implemented, communicate effectively with your team so they understand the changes you have made, why you have implemented them, and how to navigate the new warehouse layout. But you don’t need to stop there. To truly optimize your warehouse layout, you must continuously experiment with new ideas and monitor what works and what doesn’t.
Keep the effective changes, cut changes that are not helping, and keep asking for employee feedback. You may find that some of your bright ideas are not as helpful as you first thought.
How Descartes Sellercloud Helps with Warehouse Visualization
You cannot improve your warehouse layout without properly visualizing how your employees and inventory navigate your current layout. Only then can you see where the inefficiencies lie and where improvements should be made. This is called ‘warehouse visualization.’ With this information, you can experiment with different approaches and monitor how well they work. Likewise, you may uncover new issues you would never have noticed without a bird’s-eye view of your warehouse’s operation.
Descartes Sellercloud’s patented WMS, Skustack, enables merchants to do all this with the Skustack Lens feature. With Skustack Lens, you can track inventory, monitor employee performance, and save the dimensions of bins and shelves. When you save the dimensions of bins and shelves and the dimensions of your cases and products, Skustack Lens provides insight into which incoming shipments can fit where, helping you utilize every square inch of your warehouse.
Furthermore, merchants can use a 4D Scale to measure product and case dimensions and save them so they know precisely how much space is required for incoming and existing inventory. Knowing the exact product and bin dimensions helps merchants reorganize and utilize their warehouse space for inventory changes, such as incoming inventory.
Lastly, the data from Skustack can be used to see which SKUs are picked the most so they can be placed low down and easily accessible.
Book a Descartes Sellercloud demo today.
Key Points
Ready to start planning your warehouse layout? Don’t forget these key points.
- Poor warehouse layout can limit your storage capacity and make it difficult to keep up with changing demand. It can also cause fulfillment problems and risk your employees’ safety.
- Warehouse layout should consider storage needs, your workflow, safety, regulations, scalability, accessibility, required tech, and its impact on order fulfillment, to name a few.
- The most common warehouse layouts are U-shaped, L-shaped, I-shaped, and fishbone.
- Implementing the right vertical racking and properly segmenting different warehouse areas is vital to optimizing your available space.
- Skustack Lens helps optimize warehouse layout designs with warehouse visualization. Merchants can save the dimensions of products, shelves, and bins and monitor staff movements.
- The real-time data provided by Skustack Lens enables merchants to react to changes like incoming shipments. They can visualize the exact dimensions of the space and products and see exactly where they fit or how they can reorganize their inventory.