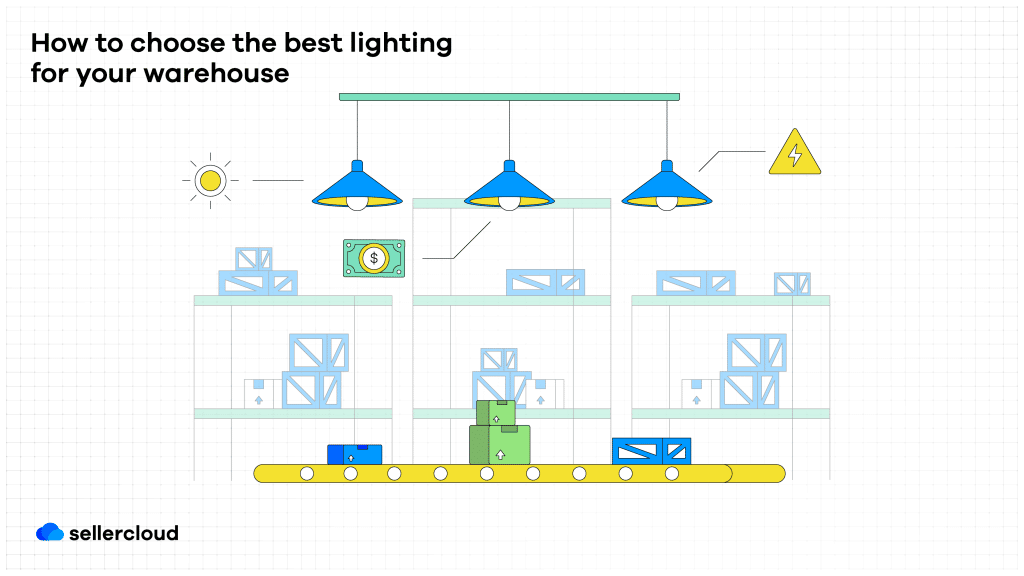
There are a lot of factors to consider when establishing your own warehouses. In other blog posts, we have discussed elements of this process, including:
- Calculating the amount of warehouse space you need
- Determining the number of warehouses you need
- Finding your ideal warehouse(s)
- Designing the perfect warehouse layout for your business’s needs
- Identifying critical warehouse roles to hire
These are all vital considerations for bringing your ecommerce warehousing operations in-house. Along those same lines, there is another key element of your warehouse decision-making that can have significant impacts on efficiency, costs, and safety: lighting.
In this post, we will discuss the pros and cons of various warehouse lighting options and best practices associated with making the right choices.
The Importance of Getting Warehouse Lighting Right
Not all warehouse lighting is created equal. There are different types, sizes, patterns, and styles of lights that need to be considered before you can settle on the ideal type of lighting for your warehouse. Moreover, different areas of your warehouse may have different needs depending on their function, layout, and workflows.
Ultimately, costs, efficiency, and safety are three of the most important considerations when it comes to running an ecommerce warehouse. All three of these elements come into play when you are making decisions about your warehouse lighting options.
Warehouse Lighting Costs
Lighting is one of the most expensive costs associated with warehouse operations. Depending on your structure’s needs, making incorrect choices about what types of lighting to install could pose a long-term drain on your operational budget. High-efficiency options, like LEDs, come with high upfront costs but save you money in the long run through lower power bills.
More traditional options like incandescent, fluorescent, and halogen lighting are relatively inexpensive by comparison, but they consume significantly more power and require more regular replacements.
Warehouse Lighting Efficiency
The power draw of your lighting setup is obviously important to consider, but there are other optimizations you should be remembering as well. Quantity, placement, and beam type all affect how well your spaces are lit. The effectiveness of your warehouse lighting plan will determine how efficiently your team can find the items and locations they need, assess products, fulfill orders, and avoid errors.
Warehouse Lighting Safety Concerns
Lastly, lighting is a core component in keeping your warehouse employees safe. Regular warehouse audits should be conducted to find and correct dark areas or warehouse zones with poor general lighting quality. There should always be a budget and plan for conducting maintenance, repairs, and replacements of defective lighting to ensure that warehouse safety is maintained.
Weighing the Pros and Cons of Your Warehouse Lighting Options
When it comes to industrial and commercial lighting, there are four distinct categories to choose from: incandescent lights, halogen lights, fluorescent lights, and LED lights. Each option has its own strengths and weaknesses depending on how and where the lighting is needed.
Incandescent Lighting
Incandescent lights are the traditional light bulbs that most of us grew up with. Electricity heats a metal filament to the point where it glows and emits light and heat. They are a simple technology that relies on inexpensive materials to produce. They are not very efficient and produce more heat than other lighting options.
Pros:
- Inexpensive to purchase.
- Widely available in multiple form factors and wattages.
Cons:
- Highly inefficient from an energy-usage standpoint.
- Short lifespan means more frequent replacements.
- Significant heat output wastes energy and creates potential hazards.
Fluorescent Lighting
Fluorescent lighting creates bright light by using electricity to spark a reaction involving gases in vacuum-sealed tubes. This is more efficient than incandescent alternatives in terms of both energy consumption and longevity. However, these tubes often contain hazardous materials, like mercury, that can pose a health and safety risk should a fluorescent bulb break.
Pros:
- A fairly economical lighting option to purchase.
- Bulbs have a longer lifespan than incandescent alternatives.
- Casts bright light.
Cons:
- It’s not the most efficient from an energy usage standpoint.
- Short lifespan means more frequent replacements.
- If bulbs break, they can release hazardous substances.
- Prone to flickering that can cause headaches and other adverse reactions for employees.
Halogen Lighting
Halogen lights rely on technology that falls somewhere between incandescent and fluorescent bulbs. The combination of a filament and halogen gas produces a light that is comparable to fluorescent lights in brightness. This process is more efficient than incandescent bulbs from an energy-usage standpoint, but halogen lights also emit significant amounts of heat.
Pros:
- More energy efficient than incandescent alternatives.
- Casts bright light.
Cons:
- Generates significant heat, which wastes energy and could cause potential hazards.
- A short lifespan means more frequent replacements.
LED Lighting
LED lighting uses small semiconductors to produce light of varying brightness, patterns, tones, and colors. The light-emitting diodes are also incredibly efficient and long-lasting compared to incandescents and fluorescents. That said, this efficiency comes at a significantly higher cost than other lighting alternatives.
Pros:
- Some of the highest-efficiency lighting options available.
- Generates minimal heat.
- Significantly more durable than lighting that relies on glass and/or filaments.
- A long lifespan means fewer replacements.
Cons:
- Higher up-front costs compared to other lighting types.
When choosing lighting for your warehouse, it’s important to consider the specific needs of your business. Some factors to consider include the size and layout of the warehouse, the types of products you are storing and shipping, and the budget you have available. You may also want to consider installing specific lighting types for specific areas or activities, such as packing stations or inspection areas.
Different Areas of Your Warehouse Have Different Lighting Needs
Some warehouses may opt to use a unified approach and outfit the entire warehouse with a consistent type and style of lighting. Still, others may choose a blended approach, tailoring specific lighting choices to specific areas and functions of the warehouse. Your ideal lighting choice for each area of your warehouse depends on the specific tasks being performed in that area and any specific safety regulations you must comply with.
Here are some general guidelines for pairing the optimal lighting choices with the different areas of your warehouse:
Lighting Your Warehouse’s Loading and Receiving Dock(s)
Your loading dock is one of the few areas in your warehouse where you must regularly contend with fluctuating natural light conditions. Reading labels, identifying products, and logging the movement of goods and equipment can all be made significantly more challenging with poor lighting.
Loading docks are also areas rife with potential safety risks due to exposure to the elements and moving vehicles. To keep things running throughout the day and night, you want to choose lights that are both bright and consistent across the day/night cycle. LEDs, fluorescents, or halogen lights can provide this in ways that incandescent cannot.
Lighting your Warehouse’s Storage Area
This is typically the largest area of your warehouse. As such, it represents one of the most significant investments in your lighting costs and the area most prone to issues. You need to get this one right. Spending more upfront to purchase LED light systems can mean significant savings month-to-month on both your energy and replacement costs.
That said, cost is only one piece of the puzzle regarding illuminating your storage areas. Light placement and pattern types matter as well. First, you need to consider the height and placement of your racks and stacks. This will dictate the ideal light patterns and placements.
Warehouse lights are traditionally advertised as casting an ‘I-pattern’ or a ‘V-pattern.’ Each has its own function, relevant to different warehouse layouts.
For warehouses with tall shelving systems, installing lights that cast an ‘I-pattern’ can make it possible to evenly illuminate the tall, narrow spaces between vertical racks. For warehouses with fewer height interferences and more of an open-concept design, a ‘V-pattern’ casts a broader light that allows for large spaces to be more evenly lit.
When it comes to strategically deciding on the physical placement of warehouse lights, placing a light source too close to merchandise can lead to damage, degradation, or even fire hazards. Similarly, tall shelving systems could potentially block light sources and create shadowy areas that impair your team’s ability to safely and efficiently store and retrieve inventory.
Lighting your Warehouse’s Picking and Packing Areas
Ideally, the areas of your warehouse where orders are picked, packed, and labeled should be some of the best-lit areas of your entire operation. Your employees need to be able to identify products and fulfill packing orders easily. Bright, clear lighting choices like LEDs and fluorescents are good choices to create even, vivid coverage that can help keep employees alert and minimize mistakes.
Lighting Your Warehouse’s Office Spaces and Common Areas
Lighting matters in the spaces off the warehouse floor as well. In fact, the lighting that you choose can go a long way in making your office space, public lobby, break rooms, and even restrooms comfortable and safe spaces for work and business. Incandescent or LED lighting options that give off light in the warmer tones of the visible spectrum can help create a more welcoming feel than the intense brightness of cooler-tone fluorescents and LEDs.
Overall, it’s important to choose lighting that is appropriate for the tasks being performed in each area of the warehouse and that meets any applicable safety regulations. It may also be helpful to consult with a lighting specialist to determine the optimal lighting choices for your warehouse.
Many lighting vendors will provide this service as part of the quoting process. For more strategies and tips for getting your ecommerce warehouse up and running as efficiently and profitably as possible, check out our Definitive Guide to Setting Up Your Ecommerce Warehouse. Furthermore, if you’re planning to move from one warehouse to another, you can check out our guide to moving warehouses.
Descartes Sellercloud has the tools and software to help you make the most out of your ecommerce warehouse operations. You can manage your inventory, process orders, and run nearly every aspect of your omnichannel business from our unified, cloud-based platform.
Contact us today to schedule a free consultation and see how our technology and expertise can supercharge the way you sell online.